
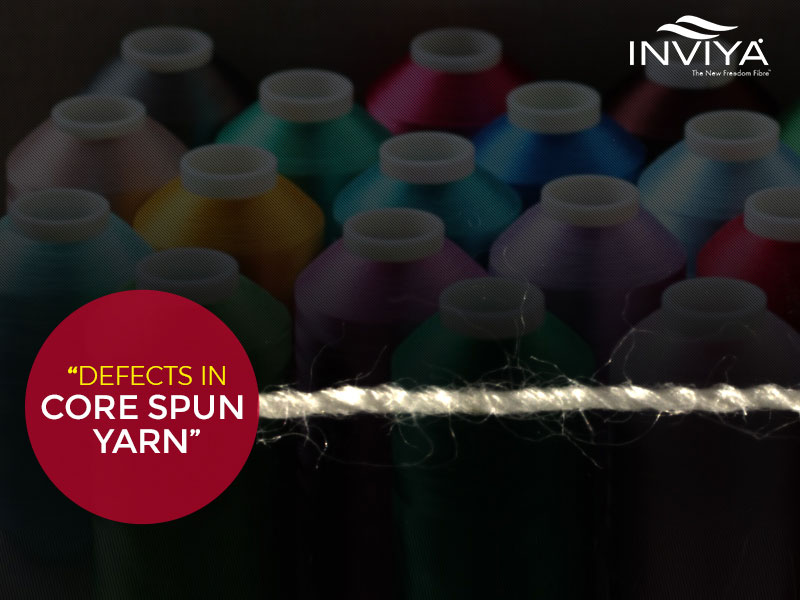
- Grin-Through — This defect is an incomplete covering of the core of spandex and is caused by improper positioning of the core with respect to roving.
- Short core voids — This defect comes in short sections (25 to 75 mm) of yarns with no stretch because the core broke after the yarn was spun. This may happen due to poor positioning of spandex yarn to roving, over-drafting of core spun yarn (use recommended drafts), poor mechanical condition of rings, excessive traveller speed, and too heavy traveller
- Long core voids — It is long section of yarn with core missing. This defect may arise due to nicked or rough guide surfaces, back drafting of spandex on the tube resulting from insufficient feed-roll contact, over drafting of core yarn and mishandling of spandex supply tubes
- Sheath Voids — The causes of this defect are breaks in roving during drafting, over drafting of roving, poor quality roving, improper position of roving allowing pneumafil to rub staple fibres and worn cots, aprons
- Selvedge curling — the selvedge of the fabric gets curled because of the yarn behavior and low weave strength of the selvedge.
- Holes in the fabric — this defect arises due to; low yarn TM (twist multiplier), strong finishing treatments (which may abrade the surface of the yarn), splice failure (low splice strength)
- Spandex miss – this is caused mainly due to splice failure and due to broken spandex (caused by surface damage)
- Cloudy fabric appearance: caused due to high short term count variations even though the average count is within the acceptable limits.
Recent Posts