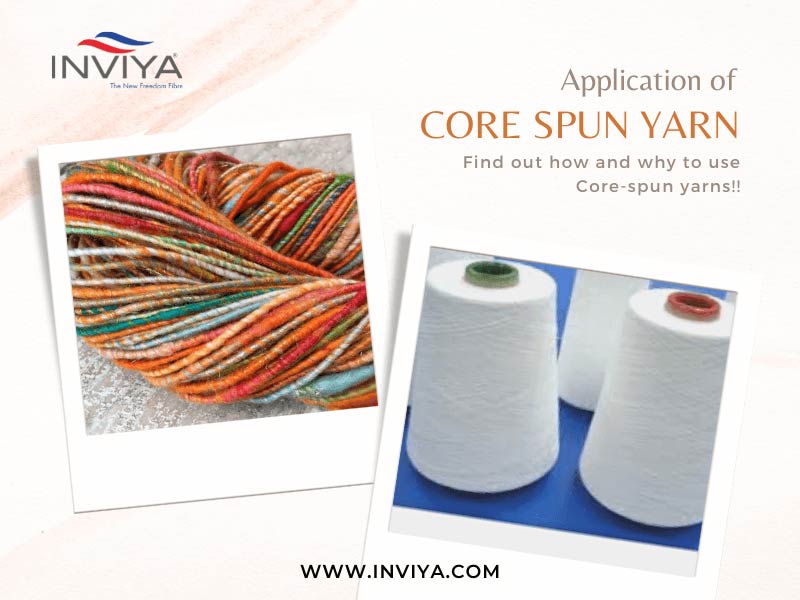
In the apparel and garment industry, denim has been a huge attractiveness with excessive capacity that makes use of it a stylish fashion everywhere. Fabrics used for denim are flexible and durable.
Denim marketplace has an awesome marketplace length at the cost of $57,312. Five million and it’s far has predicted that the denim marketplace could have an annual boom price of about6.4% as time passes by.
The denim region with the biggest contribution price to the worldwide sales with better foremost merchandise many people of all age groups will be predicted to retain in developing within the destiny jean marketplace.
With a lot of preference, the denim region has to continuously evolve the material homes to fulfill client wishes consisting of flexibility, form preservation, abrasion resistance, as well as snug to put to use in any respect times. High aggressive capacity in this region pushes the agencies to provide possibilities of various fibers; practical yarns use that makes contributions to material homes.
Core Spun Yarn is a type of fabric that is mostly used to create the majority of denim apparel. Core spun yarns are a type of fabric that is typically made by wrapping a staple polyester or cotton wrapper around a non-stop filament package deal of polyester fibers at some point of spinning, then plying those yarns into a stitching thread. The non-stop filament polyester middle makes up about 60% of the thread construction.
Why Use Core-Spun Yarn?
Core spun yarn is one of the finest fabrics out there. There are several superior fabric properties that core-spun yarn possesses, which makes it a perfect fabric to use in denim. These properties include:
- High level of tenacity, which means higher strength per length
- The strength, size, and other physical characteristics are uniformly distributed.
- A better preliminary modulus or resistance to stretching contributing to higher loop formation and decreased seam puckering.
- Superior abrasion resistance & durability
- Better ply security – less unravel-type thread breaks.
The manufacturing of fabrics like Core-spun yarns is mostly accomplished efficiently through numerous systems used to spin the fabric continuously. Each gadget has its own personal features.
The traditional ring spinning, easiest and economic systems; however, the middle positioning within the center is often seen to be a bit on the tough side. Most importantly, in the next technique, strip lower back trouble may also rise, and the middle filaments get tangled up. Nevertheless, the middle positioning may be set appropriately and mostly used to supply the commercial yarns.
Applications of Core-Spun Yarn
There are numerous applications of core-spun yarn. As threads, it can be used in leather products, mattresses, and quilts such as women’s shoes, handbags, etc. The immense strength and durability make the core-spun yarn used widely in rice bags too. There are various spinning methods of the core-spun, such as self twist spinning, vortex spinning, electrostatic spinning, ring spinning.
How are Such Yarns Made?
Core Spun Yarn threads are made by spinning 100% Polyester staple fibers into yarns, after which plying those yarns into a stitching thread. Spun Polyester threads are usually made in or three-ply structures relying on the yarn size. As a result, spun polyester threads normally have an awful lot less single give up breaking energy than this particular type of Yarns.
Dual core-spun yarn, made with its own twist, is changed into a ring spinning gadget, which changed into the design using a further gear for facilitating each fiber feeding simultaneously.
Next, each PET filament is pushed with the aid of using an advantageous feed curler separately. These additives are then made to enter the nip factor through a V-grooved curler, and each time, cotton fibers are passed in such a way that cover up those additives.
The most common approach of core-spun yarn manufacturing is via way of integrating and combining several filament packages in the shape of a ring. A spool of filament opens up on its own to enter into the filament into the tip of the drafting rollers present on the front. This method is mostly used to supply polyester or cotton stitching threads.
To produce yarns that are made stretch-to-match garments, a filament that is elastomeric is passed below. The need for such a filament yarn within the center, including cotton fiber, is broadly utilized in garb applications. Some latest trends encompass the usage of multiple center filaments included via means of cotton.