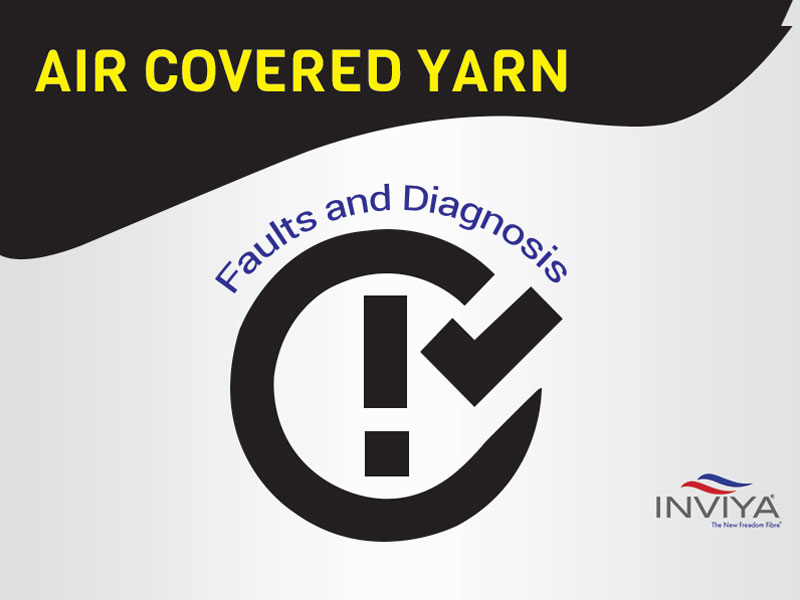
Just like any other yarn, Air Covered Yarn also experiences some faults which are caused mainly by two issues – Positional Faults and General Faults. Below are some of the faults that are seen in Air Covered Yarn.
- Filamentation:
- Positional causes:
- Damaged/worn guides
- Dirty heaters
- Damaged friction discs
- Waste on feed rollers/bowl
- Misthreading
- Mechanical damage to supply yarn
- General Causes:
- Draw ratio too high
- Heater temperature too high
- Speed ratio too high
- D/Y ratio too low
- Supply type/finish unsuitable
- Positional causes:
- High break rate
- Positional causes:
- Worn nip rollers
- Supply package misaligned
- Damaged friction discs
- Misthreading
- Damaged or badly wound supply yarn
- General Causes:
- Speed too high
- Draw ratio in correct
- D/Y ratio too high or low
- Heater temperature too high
- Ambient conditions incorrect
- Supply type/finish unsuitable
- Positional causes:
- Tight spots
- Positional causes:
- Worn nip rollers
- Incorrect threading
- General Causes:
- Unstable process specification
- D/Y not optimum
- Supply irregularity
- Positional causes:
- Dye/Bulk variation
- Positional causes:
- Heater temperature fault
- Heater cold top (dark dye)
- Damaged friction discs
- Incorrect twisting unit speed
- Damaged or worn guides
- Take-up tension variation (bulk)
- Worn/damaged nip roller
- General Causes:
- Unsuitable process specification
- Dirty heaters
- Supply irregularity
- Positional causes:
- Webbing/ overthrows
- Positional causes:
- Misaligned cradle
- Stroke too long
- Loose or worn traverse guide
- Wear or damage in traverse box
- Cradle catching on feed, back arm
- Point of origin guide not central
- General Causes:
- Take-up tension too high
- Wind angle too low
- Taper angle too low
- Radial disturbance too high
- Axial displacement very high
- Positional causes:
- Poor package unwinding
- Positional causes:
- Stroke length incorrect
- Cradle settings incorrect
- Filamentation in textured yarn
- Yarn coming out of traverse guide
- Package webbed
- General Causes:
- Take-up tension too slow
- Wind angle too high
- Taper angle too low
- Incorrect oil
- Filamentation in textured yarn
- Radial / axial disturbance link out of phase
- Positional causes: